Trying to decide which equipment to use in your plant or manufacturing process can be a headache, and choosing an air dryer for your air compressor system is no exception.
But never fear, ISC Sales is here! We put together this guide to help you to make the decision on which equipment will work best for you.
Everything you need to know about air dryers is conveniently listed here.
Jump around, find the information you need and if you still have questions give us a call. We have experts that would love to help you.
Let’s start, shall we?
1. Why Do Compressed Air Systems Need Drying?
2. What Air Dryer Do I Need for My Compressor?
3. What Are the Different Types of Air Dryers?
1. Why do Compressed Air Systems Need Drying?
There are many benefits of adding an air dryer to your application. The initial cost of adding a dryer is quickly offset by the positive impact they can have on your application.
Eliminates the Threat of Water
All compressed air systems make water.
Atmospheric air contains water vapor, which begins to condense into liquid water when the air or gas used in the compressor system cools to a temperature lower than its saturation point.
The moisture in compressed air is troublesome in manufacturing processes. The build-up of unwanted moisture causes problems with the operation of pneumatic systems, solenoid valves, air motors and it can be bad news for the process or the actual product being made.
The presence of water can:
- Remove important lubricants that prevent the increased wear of moving parts, resulting in rust
- Cause paint to change color or mess with how well it can adhere
- Cause the pneumatic controls to break down because of rust, scale or clogged openings
- Freeze inside control lines, causing faulty operation of controls
- Causes corrosion in instruments that use air, leading to inaccurate readings which either interrupts or stops production processes completely
Create Contaminant Free Plant Air
By adding a dryer for your compressed air system, your operating costs will lower. Using clean, dry compressed air prevents dirt, water, and oil from being deposited onto pipes and fittings.
The build-up of contaminants in piping causes more pressure drops, which means you get less performance efficiency from your equipment.
Rust and corrosion created by liquid water plug up valves, fittings and instrument control lines. If the water in the line freezes, the same problems with plugging are more likely to happen.
Protect Valves and Cylinders
Dirty, wet and oily air deposits make a sludge that starts to make pneumatic cylinders drag, which causes frequent maintenance on seals and bearings. Operations are slowed way down and can eventually cause downtime.
If moisture is in the system, it will water down the oil that the head and rod of an air cylinder needs to work correctly. It also corrodes the walls and slows response, resulting in a loss of production efficiency.
Rubber diaphragms and valves can stiffen up and even rupture if moisture is running through them. It can also make spools and pistons pit. Neither of which is a good thing for a smoothly running production process.
Moisture can make cylinders slow and can even cause them to get stuck, this can mean lots of costly downtime.
By keeping your compressed air supply clean and dry, these problems can be totally avoided.
Extend the Life of Air Powered Tools
Pneumatic tools need clean, dry air at the right pressure to run at their best. Dirty and wet air creates problems for how well the compressed air powered tools can work.
Overly worn parts result in sluggish operation because they begin to stick, jam and rust. This means you’ll be spending money on repairs and replacing parts.
Liquid water will wash away the oils that are needed to keep the tools working right.
Plugged lines and parts will cause a decrease in pressure and the tools will lose efficiency.
By eliminating the water from the pneumatic tool’s lines, they will perform at their highest efficiency and the life of the tool will be extended significantly.
Create Optimal Instrument Air
Moisture and particles caused by corrosion can damage transmitters, relays, integrators, converters, recorders, indicators and gauges.
Even a little moisture passing through these sensitive systems can cause big problems with process controls and malfunctions.
Instruments and pneumatic controllers have to have clean, dry air to operate efficiently, especially in applications like textile mills, chemical and petrochemical plants, power plants and most general manufacturing plants.
The Instrument Safety Society of America (ISA) has outlined quality standards for instrument air in the ISA-S7.3. A copy of this list can be purchased from their website, or to save time and money, you can call up one of the experts at ISC Sales. They will be happy to help you determine the air quality needed for your pneumatic processes.
Preserve the Quality of End Products
If compressed air lines used in food production get a lot of moisture and oil in them, it can contaminate the end product, ruining it. No one wants to create faulty end products!
Moisture in control line air can cause water-logged paint, the wrong blends in liquor and the wrong mixture of ingredients in food products.
In paper production processes, air is used to position or move paper, water can make the paper dirty or keep ink from sticking to the page.
It is important to have clean and dry air for these processes to prevent damaging the end products and the loss of profits.
2. What Air Dryer Do I Need for My Compressor?
If you know the answers to the four major considerations listed below, it can make the decision process a cake walk.
1. Determine the Specific Uses of Compressed Air
Air dryers should be selected by what their end use will be. The amount of moisture that is okay for one application may not be a good fit for another.
No matter how advanced the technology is, there will always be some moisture present even after air has been passed through a dryer. Even the Atacama Desert, the driest place in the world, has a small amount of moisture in the air.
All dryers have varying degrees of drying power, also called pressure dew point availability. By knowing the specific dew point that is required for your application, you will avoid over buying and getting a system larger than what you need that has higher equipment and operating costs.
If you’d like to more information on what dew point is and to learn how to calculate it, please visit our blog article, “What’s Dew Point? (A Must-Read For Compressed Air)”
2. Find the Operating Temperatures
You have to know the end use of the air and the temperature at which it has to work to be sure that the air will remain dry enough for use in the application.
Operating temperatures can be tricky.
Some system’s needs can vary by season. In summer, many applications do not require low dew points but in winter the temperature of the cooling medium generally needs to be lower.
It is common for equipment to be located outside the building and for lines to run throughout the facility in many chemical processing plants, refineries and power plants. This means there are two different temperatures that the line air must operate at in the same system.
Temperature can change drastically from day to night. A dryer that is perfect for daytime temperatures may not be able to handle the dip in temperature during the night.
Condensation and freezing are the main considerations that should be made for specifying which air dryer will work best for you. Keep all of this in mind when selecting your perfect air dryer.
3. Learn the Actual Performance
Compressed air dryers are typically based on a standard set of conditions. They are commonly rated to reach a specific moisture level for a certain volume of air flow.
This rating is usually 100 degrees Fahrenheit saturated inlet air temperature and 100 PSIG operating temperature.
Nominal flow rating is a great place to start, but it is important to know how the equipment will actually perform under the specific conditions in your application.
It’s never a good time to buy something new, take it home, and realize that the sweater you loved is three sizes too big. Believe me, you don’t want the same situation with expensive manufacturing equipment.
4. Recognize Each Use
Plant air and powering instruments aren’t the only applications that use air dryers to remove moisture and lowering dew point.
Air that is used in low-temperature processing, like the liquefaction of nitrogen or oxygen can form ice on cooling coils. This means that processes have to be shut down to defrost the equipment. The lower the moisture content of air means the longer the defrosting process will take.
For these and other applications, the compressed air has to be free from liquid water but it also has to have a minimum content of water vapor- which sounds really complicated but it can be done.
For railroad cars that have to be filled or charged with non-reactive gas to safely store caustic chemicals, it is especially important for the compressed air to have the correct moisture content to prevent severe corrosion. For example, if chlorine combines with water vapor it can form hydrochloric acid, which is as destructive as the name sounds.
If moisture is present in the compressed air used in testing chambers, the water can have the same detrimental effect as bullets expelled by a machine gun. This can obviously cause some problems in the testing process, including destroying the model you’re testing.
If you know the end use of the compressed air that is being produced in your system, it is easier to determine which specific requirements you will need the air dryer to perform at. No application is exactly the same.
3. What Are the Different Types of Air Dryers?
All right, so now you have all the information you need and you know the demand of the air dryer.
You are one step closer to buying the best air dryer for your compressor system.
Now to decide which type and technology of air dryer is the best choice for you. Let’s dive into how each type works and its advantages and disadvantages.
Regenerative Desiccant Types
1. Moisture-laden compressed air enters the dryer.
2. Coalescing prefilter removes bulk liquid to protect the dryer.
3. Air enters the drying tower where moisture is adsorbed as it flows through desiccant media.
4. Particulate after-filter protects pneumatic tools and equipment.
5. Dry air flows to the downstream process.
6. A portion of air is directed to purge tower.
7. Air flows through purge tower as the desiccant is regenerated.
8. Moisture is exhausted to the atmosphere.
Regenerative desiccant dryers use a desiccant medium to adsorb the water vapors that are in the compressed air stream.
Adsorption means the moisture collects in the thousands of small pores inside the desiccant bed, adhering to the desiccant.
The composition of the desiccant doesn’t change its composition and the moisture collected can be flushed out of the system with a process called regeneration.
Regenerative desiccant dryers are usually made with two towers.
The desiccant in one tower dries the air from the compressor, while the desiccant in the other tower is being regenerated. Which means the moisture is removed by expanding air to the atmosphere as it passes over the desiccant beads.
Regenerative desiccant air dryers use different methods during the regeneration process including externally heated, blower purge and heatless pressure swing technologies.
The benefits and disadvantages of regenerated desiccant air dryers are….
+ Very low dew points can be achieved without the chance of freezing-up
+ Moderate cost of operation for the dewpoints that can be achieved
– A high initial capital cost
– Replacement of the desiccant bed, usually between 3 to 5 years
– Oil or lubricants can cover the desiccant material, which makes it useless if pre-filtering is not maintained
– Purge air is typically required
Heated Dryers
Externally heated regenerative desiccant dryers use temperature swing adsorption (TSA). This means that the purge air has been heated to the desired temperature before it passes through the desiccant bed.
MODEL | PHOTO | IN/OUT CONNECTIONS – NPT/FLG | WEIGHT | WARRANTY |
---|---|---|---|---|
Nano D5 Externally Heated Twin | ![]() |
1” to 6” | 610 – 8300 lbs | 5 years |
Heated Blower
Heated blower desiccant air dryers use an external blower and heater to force hot atmospheric air into the regenerating desiccant bed.
MODEL | PHOTO | IN/OUT CONNECTIONS – NPT/FLG | WEIGHT | WARRANTY |
---|---|---|---|---|
Nano D5 Blower Purge | ![]() |
2” to 8” | 2890 – 27000 lbs | 5 years |
Blower Purge Regenerative Air Dryer
** Can be adjusted for heat or just blower |
![]() |
1”to 6” | 855-11200 | N/A |
Heatless Pressure Swing
Heatless regenerative desiccant dryers is a mouthful, but they work just like the name implies. They don’t use any heat either externally or internally. Instead, they use pressure swing adsorption (PSA).
PSA is when moisture is desorbed from the regenerating vessel, using rapid depressurization with a sweep of dry purge air.
Heatless type desiccant air dryers can be designed to operate pneumatically for remote, mobile or hazardous locations.
MODEL | PHOTO | IN/OUT CONNECTIONS – NPT/FLG | WEIGHT | WARRANTY |
---|---|---|---|---|
Nano D1 Modular Desiccant Dryers | ![]() |
3/8” to ½” | 18-56 lbs | 5 years |
Nano D2 Modular Desiccant Dryers | ![]() |
1” | 88-247 lbs | 5 years |
Nano D3 Modular Desiccant Dryers | ![]() |
2” to 2 ½” | 212-1110 lbs | 5 years |
Nano D4 High Pressure Compressed Air Dryer | ![]() |
½” to ¾” | 220-915 lbs | 1 year |
Nano D4 Compact High Pressure Compressed Air Dryer *** | ![]() |
½” to ¾” | 220-915 lbs | 1 year |
Nano D5 NHL heatless | ![]() |
1” to 4” | 650-8100 lbs | 5 years |
Heatless Regenerative GPS Series | ![]() |
½” to 6” | 217 – 6950 lbs | 2 years |
Heatless Regenerative GEH Series | ![]() |
1” to 6” | 840 – 10945 lbs | 2 years |
*** These dryers are usually built to specification so any additional will match these specs
Refrigerated Air Dryers
Refrigerant air dryers work like the air conditioner and refrigerator that you have at home. They reduce moisture by cooling the air or gas and condensing the water vapors that are there.
Once the water vapors are condensed to a liquid, the moisture can be collected and gotten rid of through a designated drain.
The air’s temperature is lowered by coolants that keep the system in a controlled environment.
They come in two varieties, cycling and non-cycling.
The benefits and disadvantages of refrigerated air dryers are….
+ Low, initial capital cost
+ Low operating cost
+ Minimal maintenance costs
+ Isn’t easily damaged by oil in the air stream, but filtration should still be used for some systems
– Limited ability to drop dew point
Cycling
1. Moisture-laden compressed air enters the dryer.
2. Passes through precooler.
3. Flows through the chiller.
4. Continues to the thermal reservoir where the part is stored.
5. Some air carries on towards the compressor.
6. Makes its way through the evaporator.
7. Passes through a drying filter.
8. The thermostatic expansion valve releases refrigerant as the air passes through.
9. The air is directed to the thermal reservoir.
10. The circulator pump directs the air.
11. The air reaches the chiller passing through it.
12. A moisture separator removes the liquid from the Air.
13. The air reaches the preheater/ precooler.
12. Dry air exits the dryer.
Cycling refrigerated air dryers, also called thermal mass dryers, store cold energy and only use it as it is as needed. This does a great job conserving energy.
The benefits and disadvantages of cycling refrigerated air dryers are….
+ Energy savings at partial and zero air flow
+ Will adjust to the demand and increase or decrease cooling capacity according to air use
– Dew point swings
– Increased size and weight to accommodate the heat sink mass
– Increased capital cost
MODEL | PHOTO | IN/OUT CONNECTIONS – NPT/FLG | WEIGHT | WARRANTY |
---|---|---|---|---|
Nano R1 Cycling | ![]() |
½” to 4” | 82-3100 lbs | 2 years |
Nano R2 High-Temperature Cycling | ![]() |
½” to 2 “ | 82-385 lbs | N/A |
Non-Cycling
1. Air enters the non-cycling refrigerated air dryer.
2. The air flows through the precooler/ reheater.
3. Enters the evaporator.
4. The liquid is extracted through the moisture separator.
5. Air exits the air dryer.
6. Some air is sent to the suction accumulator.
7. Then passes through the compressor.
8. Makes its way to the condenser.
9. The liquid from the evaporator goes to the liquid receiver.
10. Some air flows into the hot gas valve and into the evaporator.
11. Some air flows into the expansion valve that releases refrigerant and then is released into the evaporator.
Non-cycling refrigerated air dryers run non-stop and dry compressed air whether there is a demand or not.
The benefits and disadvantages of non-cycling refrigerated air dryers are….
+ Extremely reliable
+ Low maintenance costs
+ Minimal dew point swings
+ Refrigerant compressor operates continuously
– No energy savings at partial and zero air flow
MODEL | PHOTO | IN/OUT CONNECTIONS – NPT/FLG | WEIGHT | WARRANTY |
---|---|---|---|---|
Non- Cycling Refrigerated ERF Compressed Air Dryers | ![]() |
½“ to 6” | 105-321 lbs | 5 years |
Non- Cycling Refrigerated GRF Compressed Air Dryers | ![]() |
3/8” to 4” | 59-3200 lbs | 5 years |
R2 High-temperature Direct Expansion Compressed Air Dryers | ![]() |
½” to 2” | 82-385 lbs | 5 years |
R4 Direct Expansion Refrigerated Compressed Air Dryers | ![]() |
½” to 10” | ½” to 10” | 2 years |
5. What Did We Learn?
Wow, that was a lot of information! Let’s break down what all you’ve learned about air dryers.
- All air compressors create liquid water as they compress air for production use. It is important to get rid of this water to…
- Prevent damage to equipment
- Create contaminant-free plant air
- Protect valves and cylinders
- Extend the life of air powered tools
- Have the best air for instrument use
- To determine which air dryer will work best for your compressor you should…
- Determine the specific uses of compressed air
- Find the operating temperatures
- Learn the actual performance
- Recognize each use
- There are two types of air dryers carried by ISC Sales, regenerative desiccant type and refrigerated air dryers.
Still feeling a little fuzzy on which air dryer to choose? Don’t worry, we got you.
Call one of our compressed air experts today and put your doubts to rest. They can answer any of your questions and get you set up with the best equipment for you.
Call ISC Sales today at 877.602.0010 to get a free quote or to ask about our lineup of industrial equipment. You can also request a quote online, HERE.
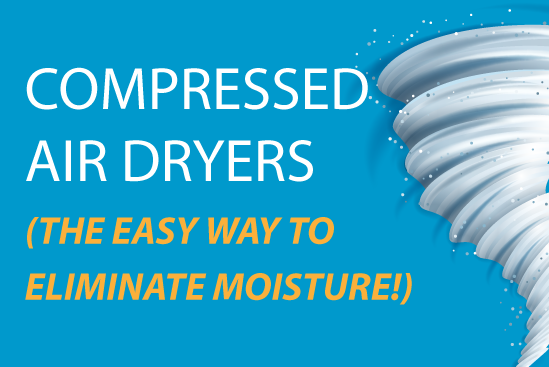
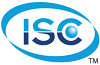